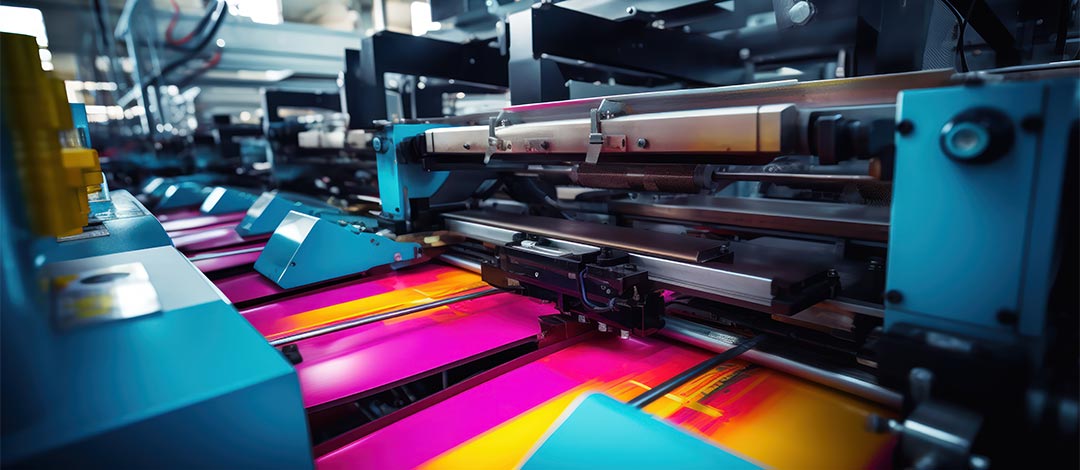
Offset printing is a popular and widely used printing technique, known for its high quality and consistency. However, even experienced operators of offset printing machines can make mistakes that affect the final product. Understanding these common mistakes and knowing how to avoid them is crucial for anyone in the printing industry. Whether you're using a large press or a mini offset printing machine, these tips can help ensure a smooth printing process.
Incorrect Ink Density
Mistake : One of the most common issues in offset printing is incorrect ink density. Too much ink can cause smudging and drying problems, while too little can result in weak, faded prints.
Solution : Regularly check and adjust the ink density settings on your offset printing machine. Use a densitometer to measure ink density accurately and make necessary adjustments to maintain the desired color consistency.
Poor Registration
Mistake : Poor registration occurs when the different colors in a print job do not align correctly, leading to blurry or double images.
Solution : Ensure that your mini offset printing machine is properly calibrated. Regularly check the alignment settings and make fine adjustments as needed. Additionally, using high-quality plates and ensuring they are correctly positioned can help maintain proper registration.
Paper Misfeed
Mistake : Paper misfeed can cause jams, uneven printing, and wasted materials.
Solution : Regularly inspect and clean the paper feed system of your offset printing machine. Ensure that the paper is properly loaded and that the rollers and guides are free from dust and debris. Use high-quality paper that is appropriate for your specific machine to reduce the chances of misfeeds.
Inconsistent Water Balance
Mistake :In offset printing, maintaining the right balance between ink and water is crucial. Too much water can dilute the ink, while too little can cause the ink to dry out on the plate.
Solution : Regularly monitor the water levels and adjust the dampening system accordingly. It's also important to use the correct type of fountain solution recommended for your offset printing machine to achieve the optimal water balance.
Plate Wear and Tear
Mistake :Plates can wear out over time, leading to poor print quality and increased downtime.
Solution : Regularly inspect the plates for signs of wear and replace them as needed. Proper storage and handling of plates can also extend their lifespan. Ensure that the plates are correctly mounted and that the blanket and impression cylinders are properly maintained.
Inadequate Maintenance
Mistake :Neglecting regular maintenance can lead to a host of problems, including ink smearing, paper jams, and mechanical failures.
Solution : Follow a strict maintenance schedule for your mini offset printing machine. Regularly clean all components, check for any signs of wear, and lubricate moving parts as recommended by the manufacturer. Keeping your equipment in top condition is essential for preventing issues and ensuring high-quality prints.
Color Inconsistencies
Mistake : Inconsistent color can ruin a print job and lead to dissatisfied customers.
Solution : Use a color management system to ensure color consistency throughout the print run. Regularly calibrate your offset printing machine and monitor the color output using color control strips. Adjust the ink settings as needed to maintain uniformity.
Conclusion
Avoiding these common offset printing mistakes can save you time, money, and frustration. By regularly maintaining your offset printing machine, carefully monitoring the printing process, and making necessary adjustments, you can achieve high-quality prints consistently. Whether you're operating a large press or a mini offset printing machine, these best practices will help you produce excellent results and keep your customers satisfied.